Sturm und Regen prägte den NRW-CUP 2025 und dennoch reisten von 19 angemeldeten Teams dann 13 final an und stellten sich der Herausforderung des Wetters. Der MBG Bocholt hat souverän die eranstaltung unterstützt und ein Dank an alle, die mitgemacht haben. Kameradschaft und Teamgeist standen im Vordergrund und die Flugleistungen suchen ihresgleichen.
Bei den Bedingungen nicht einen Abbruch zu verzeichnen, spricht für sich. Danke an alle, die sich vor und hinter den Kulissen eingesetzt haben und auch danke an die zahlreichen Zuschauer.
Vielleicht mal aktiv mitfliegen beim nächsten NRW-CUP 2026 in Eversberg.
Wir sehen uns …
Naechste Segler-Cup Wettkampf
Datum folgt
Eversberg in 2026?
Ergebnisse
Bocholt 2025
2025
Aktuelle Fotos
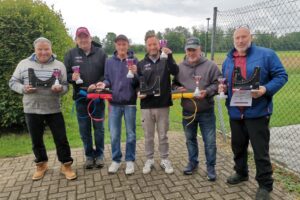
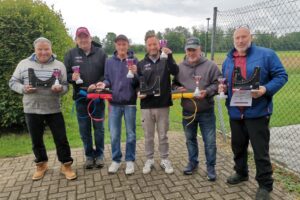
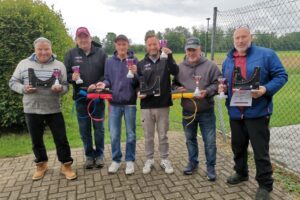
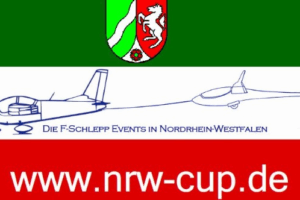
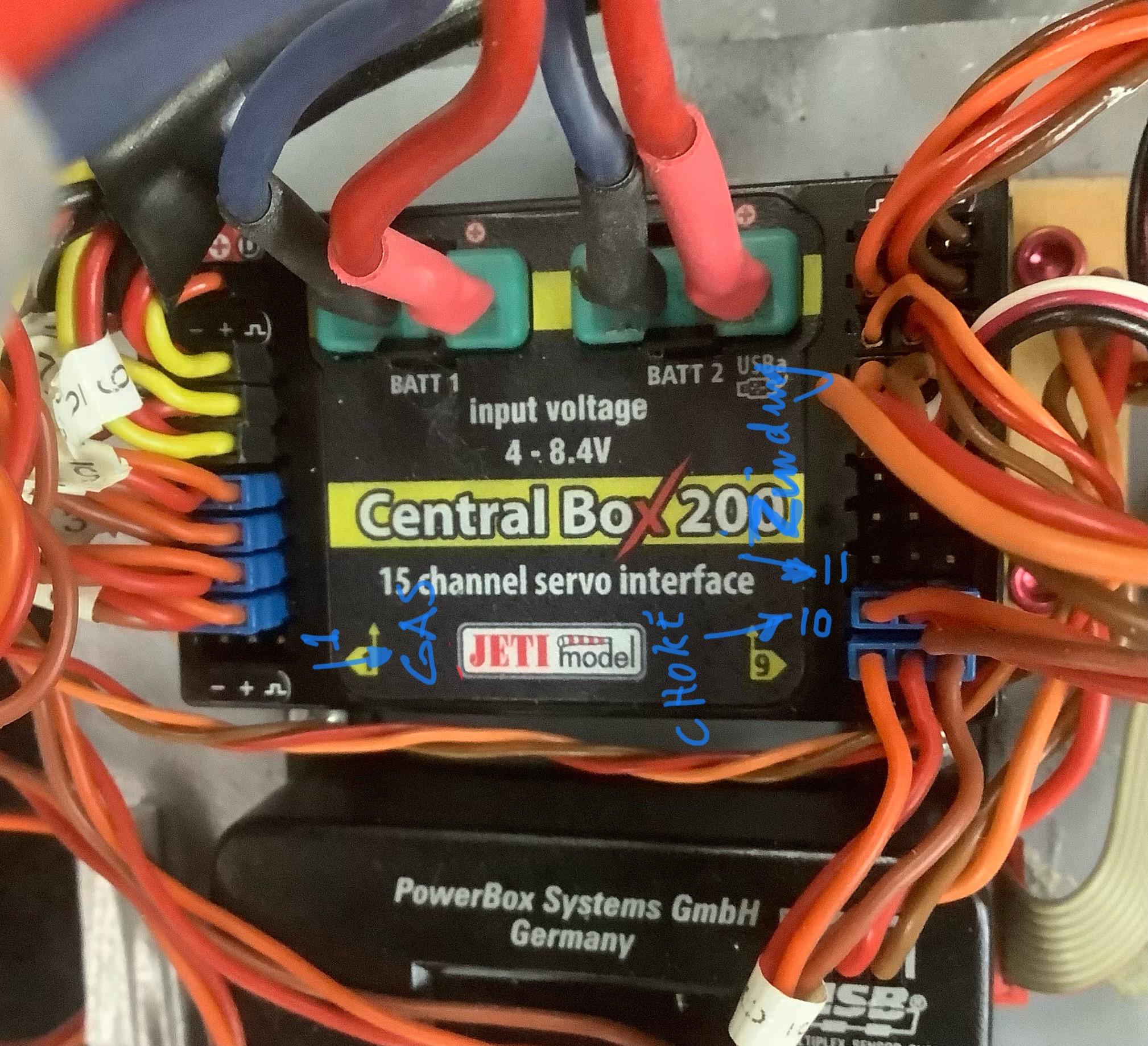
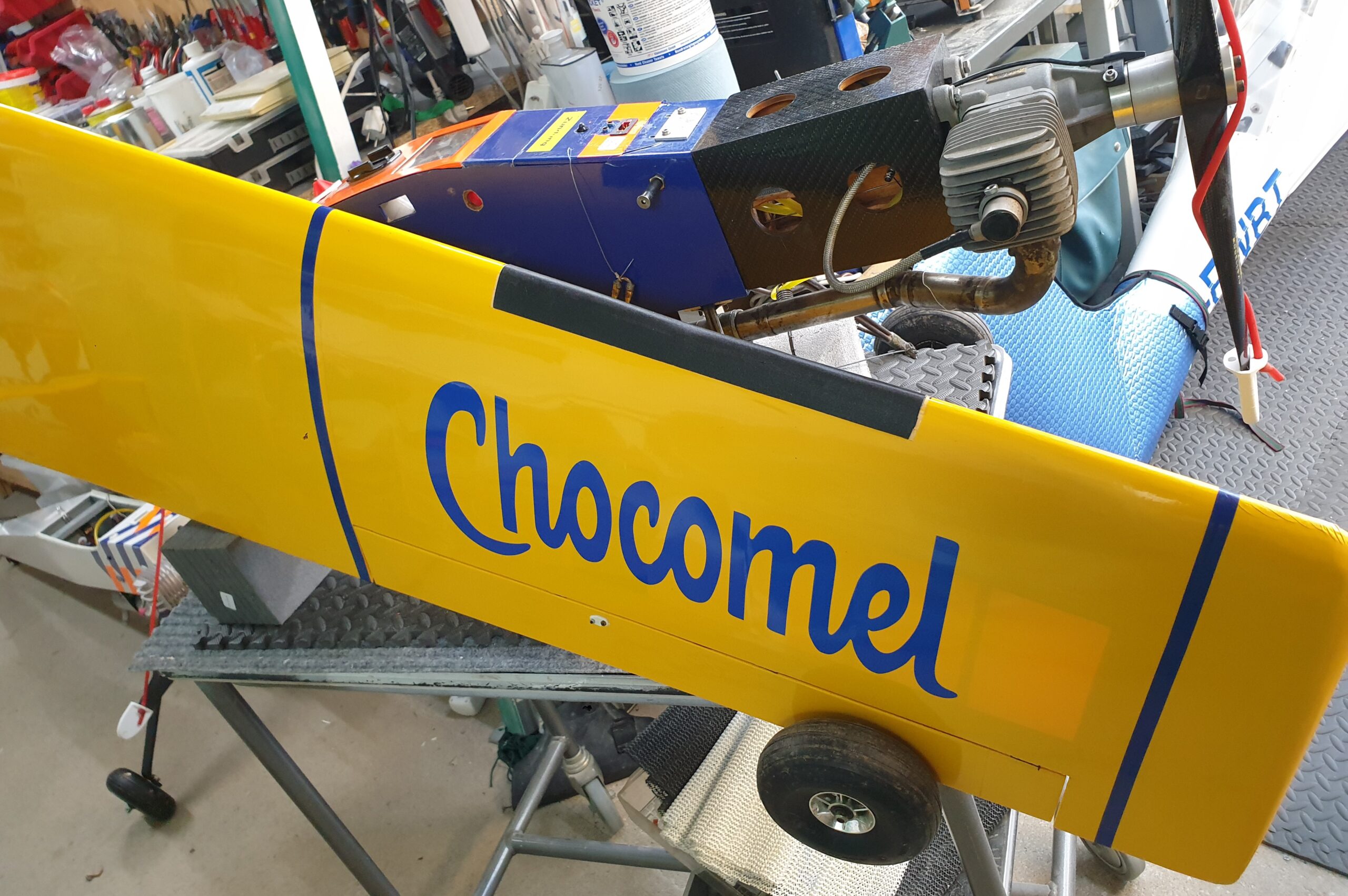
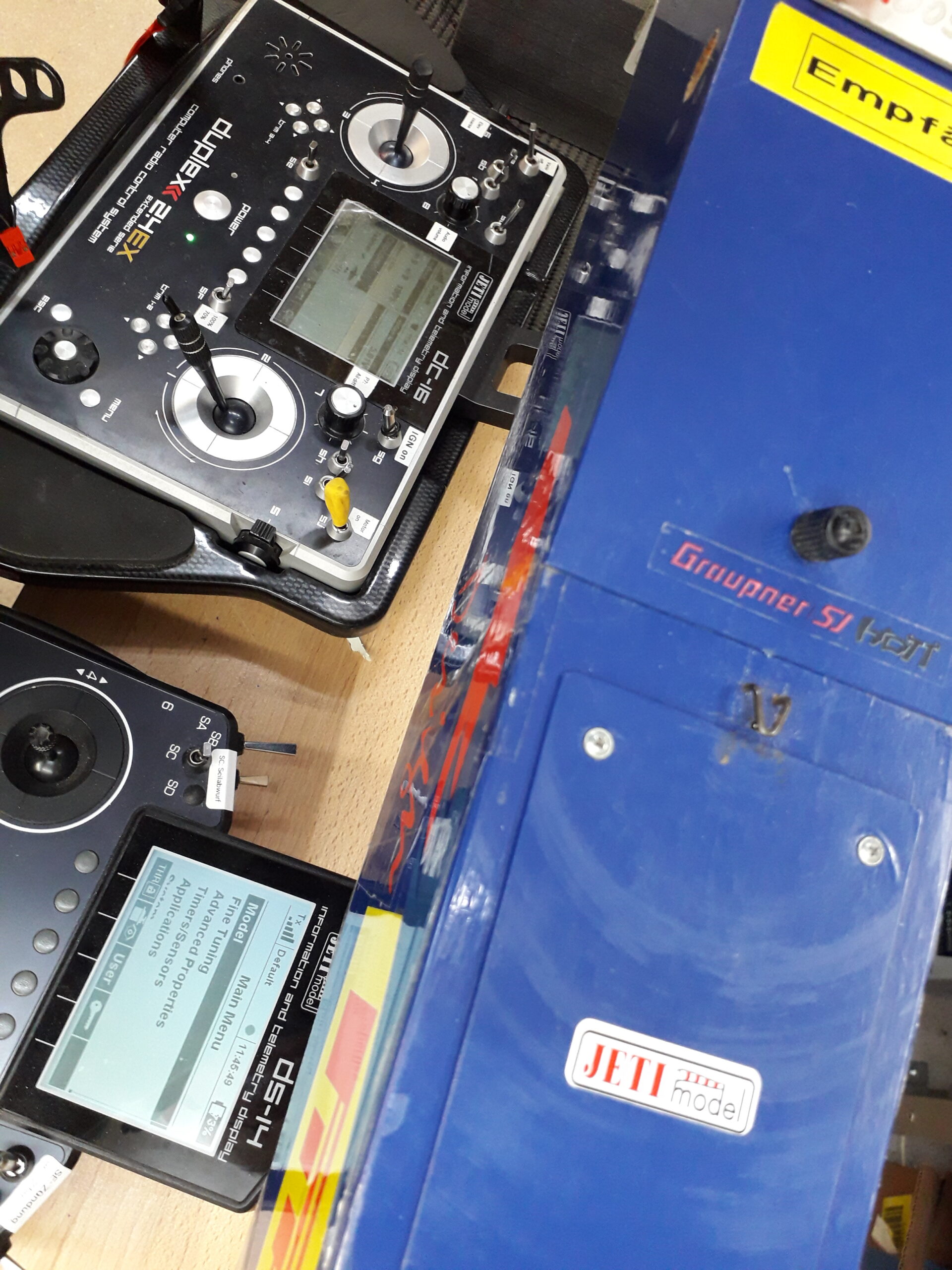
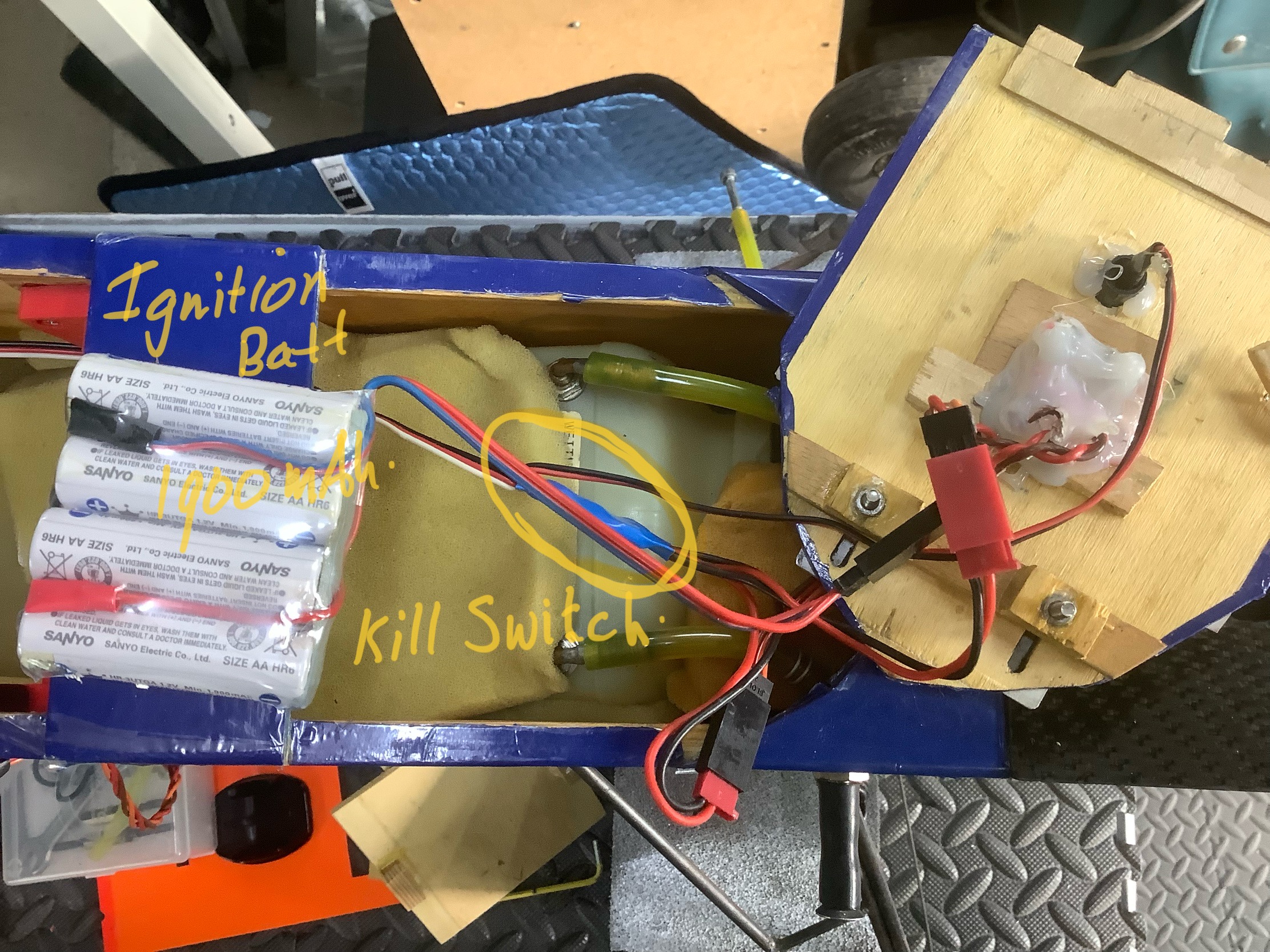
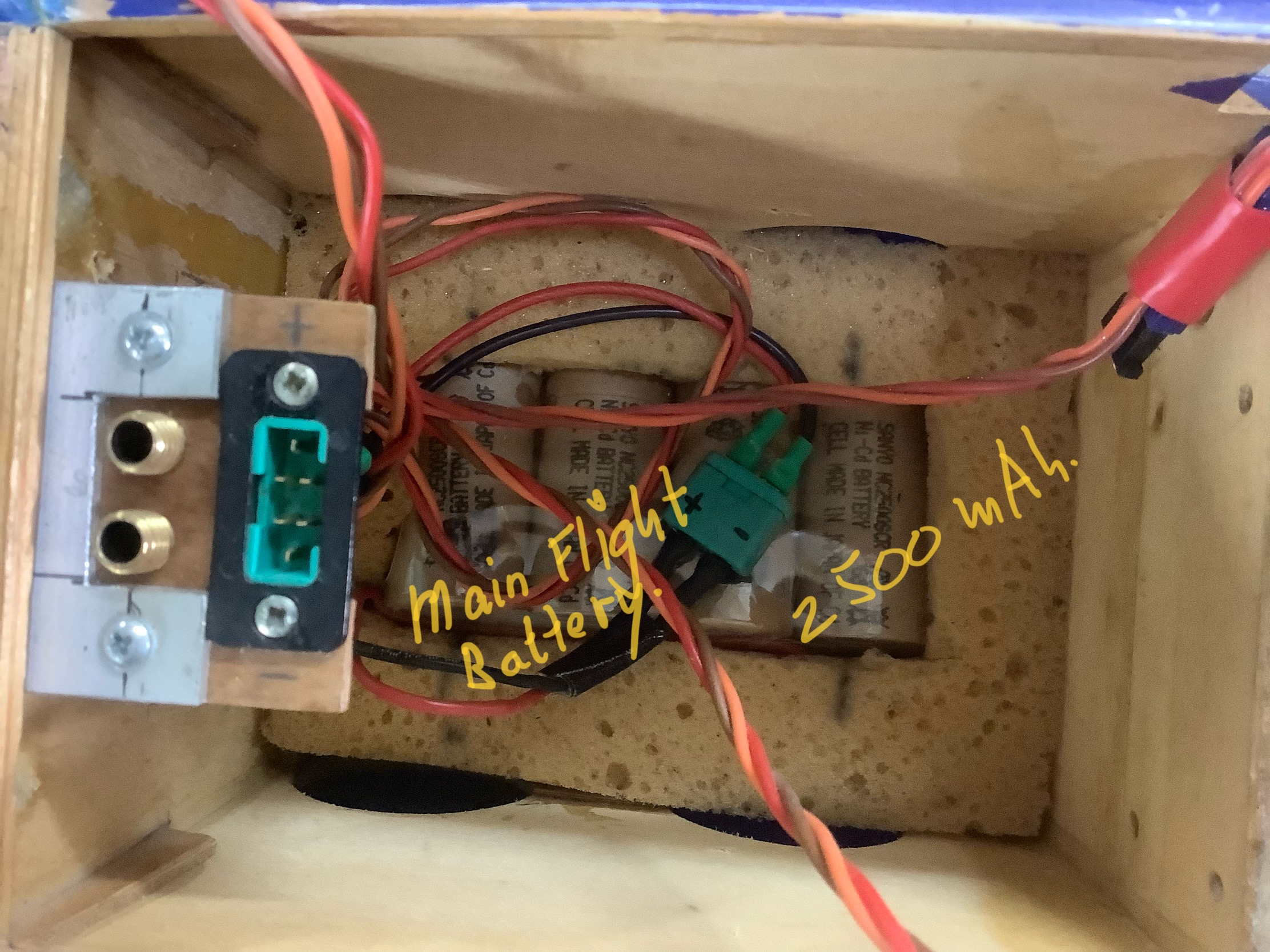
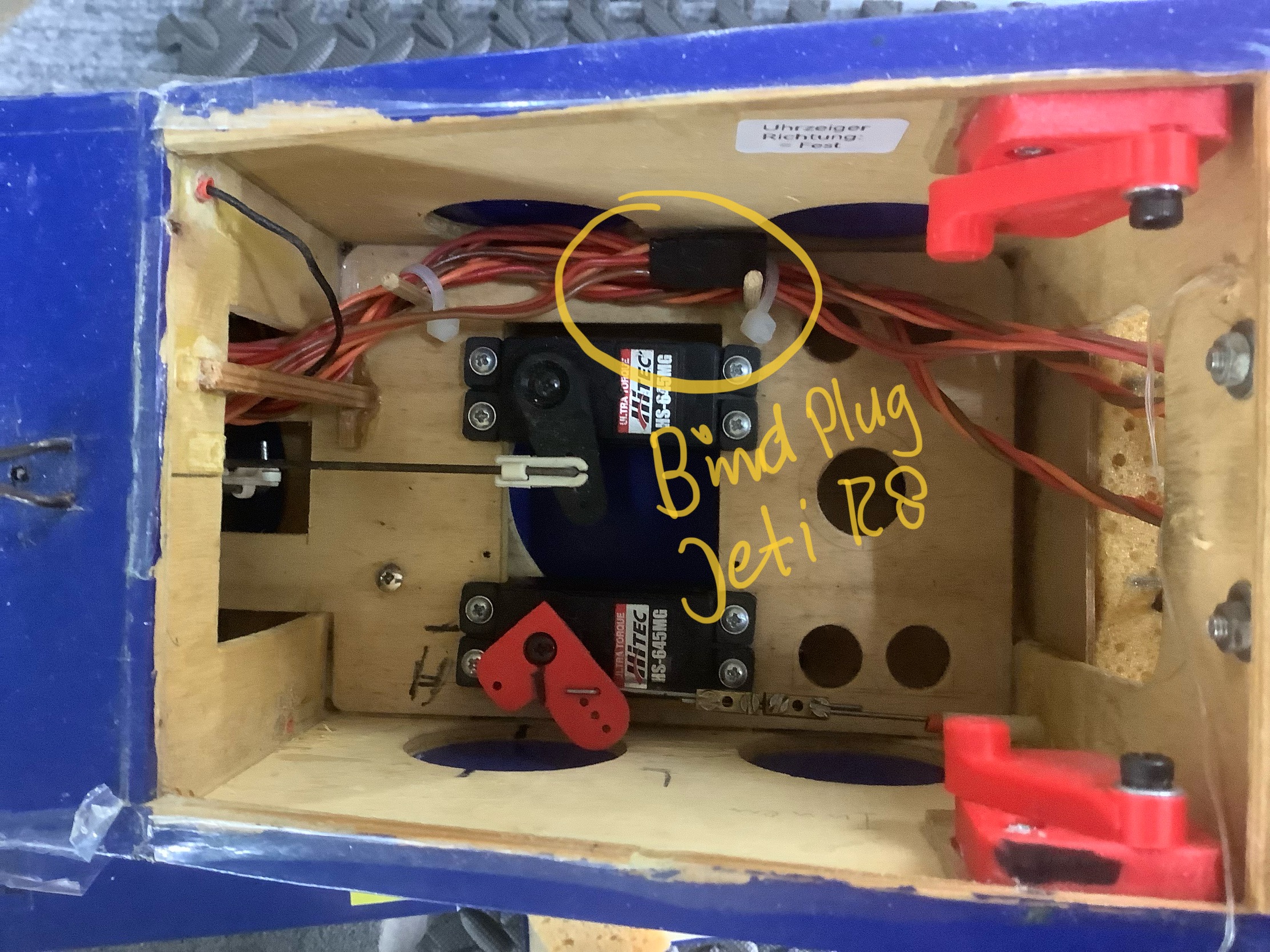

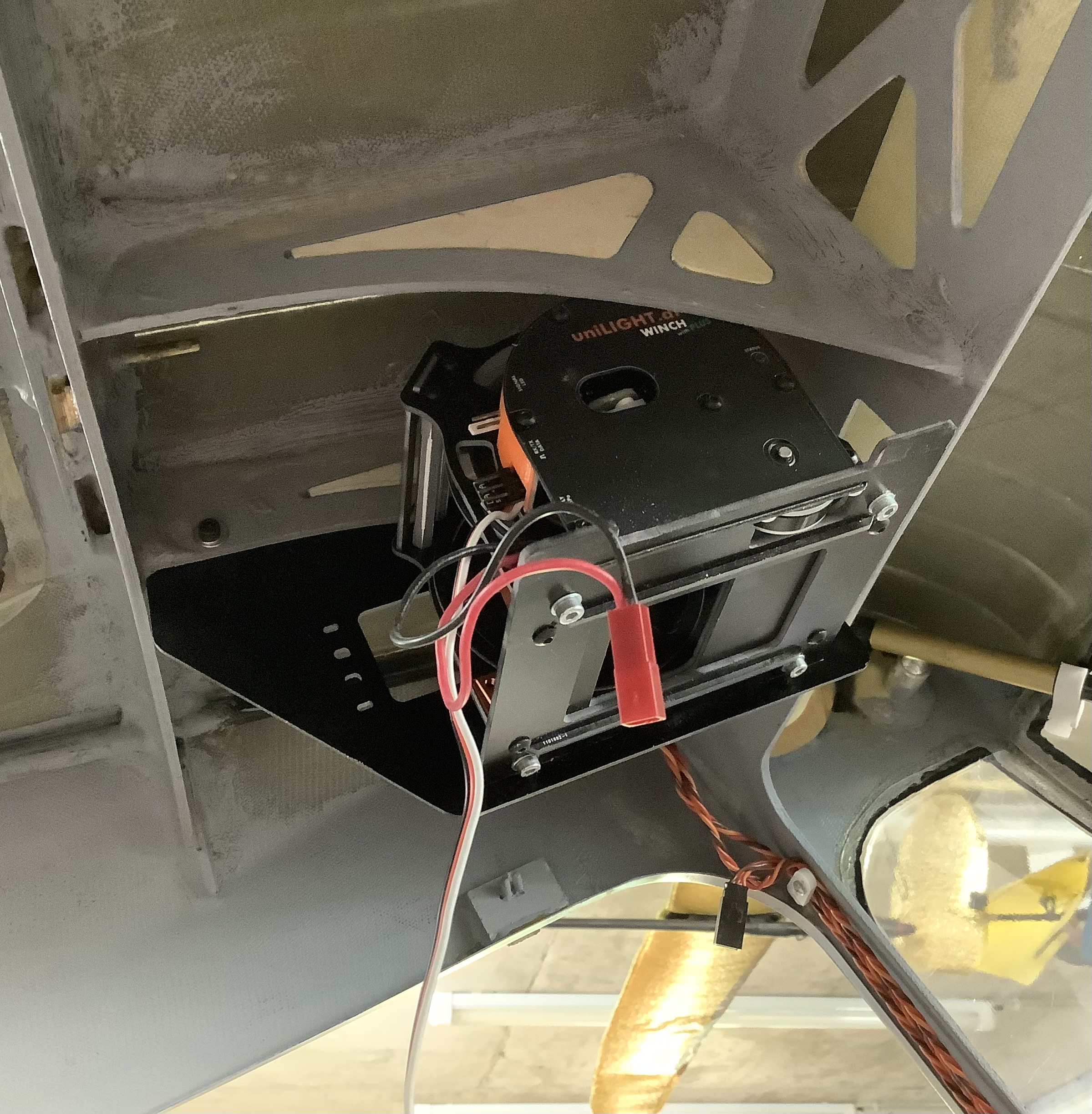