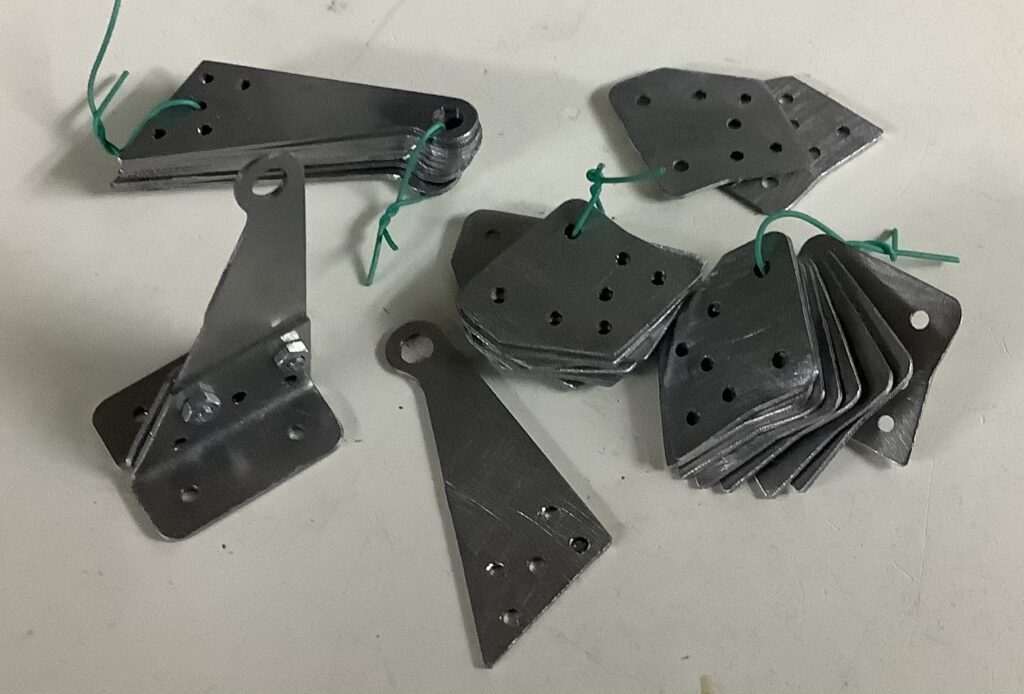
The ailerons contain quite a lot of parts. Apart from hinges, there is also a link to drive the top wing aileron. And the link to the bell-crank that is connected to the control stick.
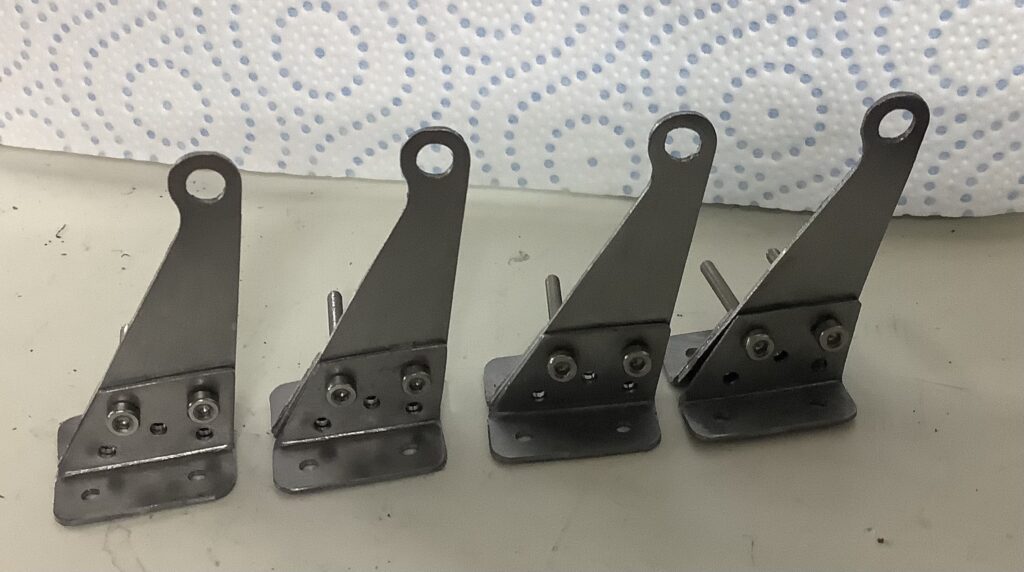
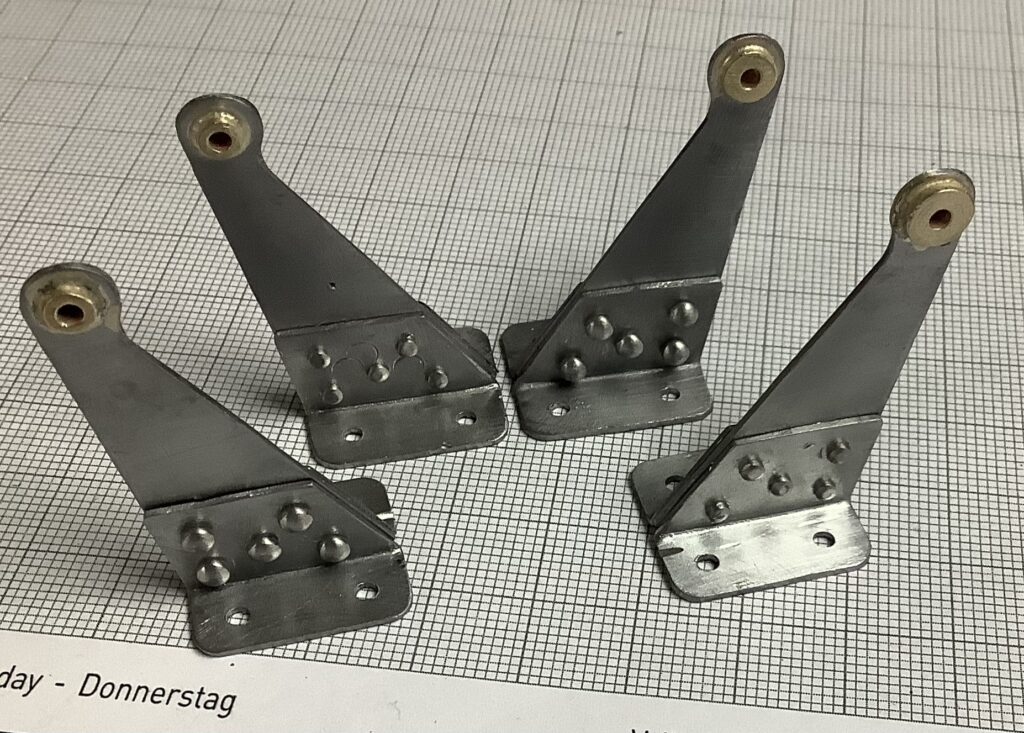
I started using a 1.5mm bit for cutting, it allows a higher spindle rpm, and better cutting of holes. Using the 2 mm bit to drill the holes was not really a good idea. Milling cutters are not drills! Also had to reduce the cutting depth per pass to max 0.3mm. A cnc router designed for wood does not have the stiffness do do any more. (At least mine does not) So with these settings and mild steel, things go great. The material for these parts is stuff from the local DIY shop, supposedly 1 mm thick. It’s more like 0.9, but I’m not complaining.
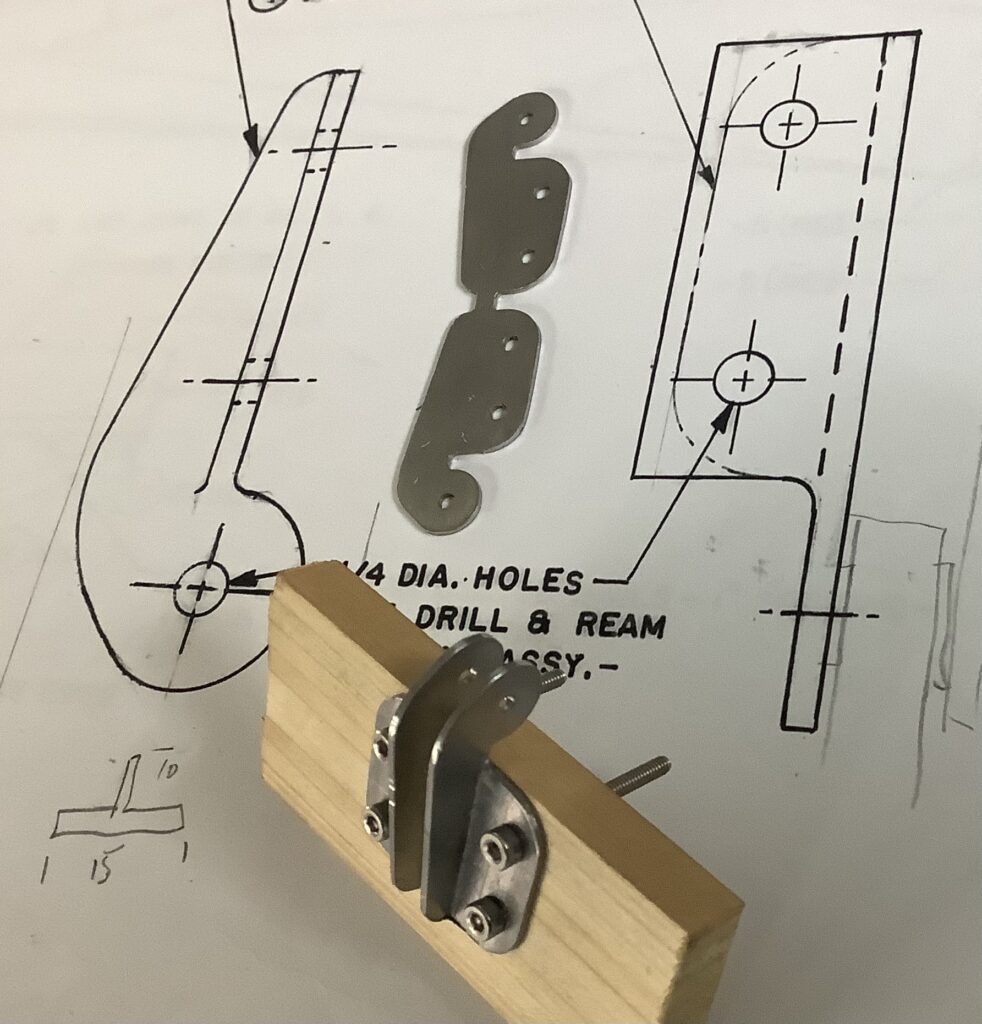
Anyways, just for reference: The original material is listed in ‘Standard Aerospace Extruded Shapes’, these ones start life as ‘AND10136-2403’ (AND stands for Army-Navy-Drawings.) It’s an aluminium T-profile to you and me. Finding out how it is supposed to be made makes it easier to make something that ‘will be close enough’.
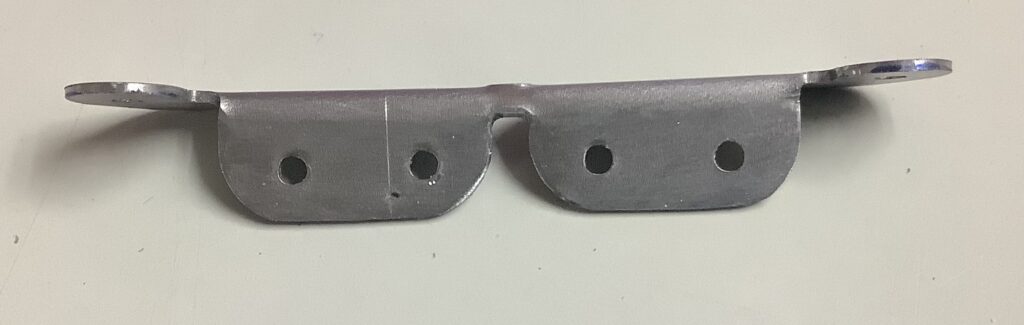
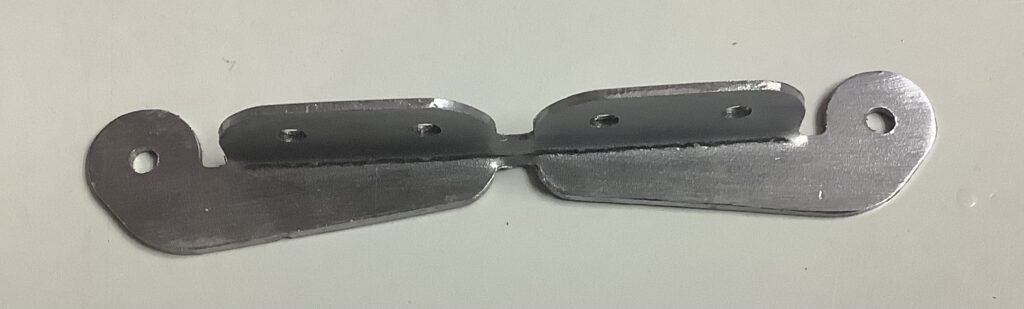
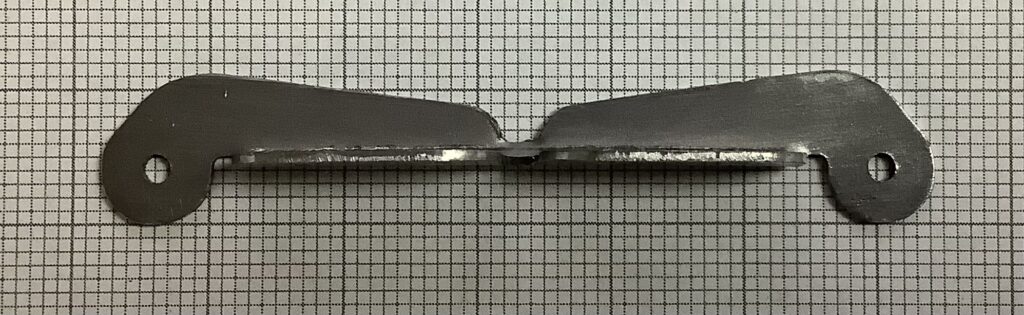
The result after paying close attention to alignment and clamping. This will do. Make a few more and on to the next step!
The reason I have 2 pcs joined is that I use 2 mm drill bits stuck through the outermost holes to align the blanks before bending. This ensures (hopefully) that that both end up equal.
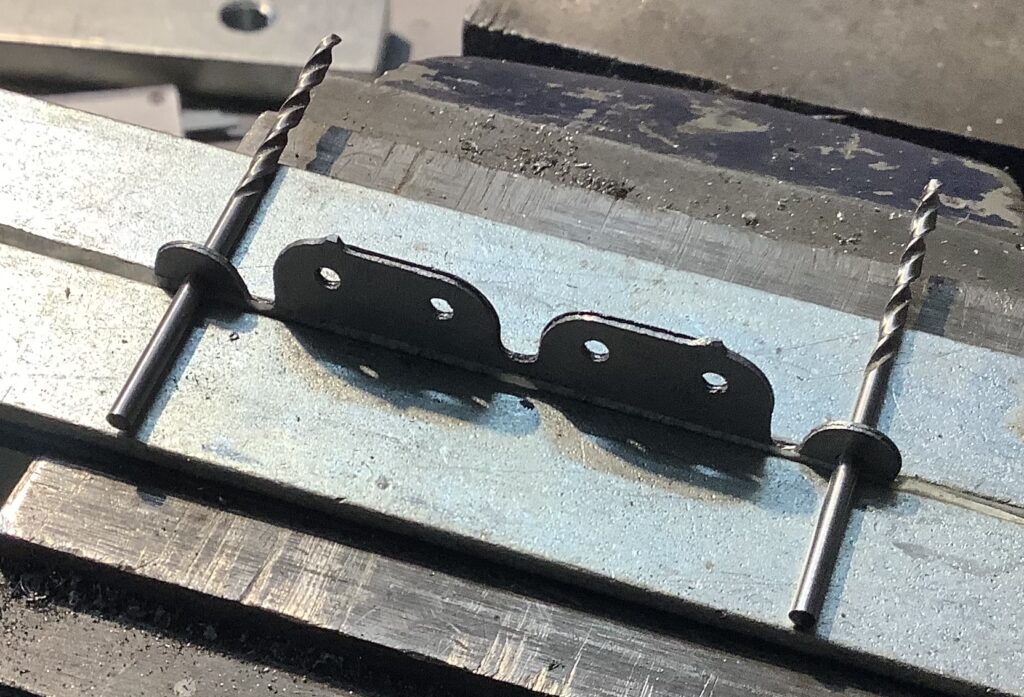