What took you so long? No idea.. More then 10 years ago I got myself a CNC-router with the idea that I would be able to metal metal parts. I’ve used it up to now mostly for non-metal parts. But retirement has given me enough time to finally sort things out. That and a better understanding of materials, cutting speeds etc. And after the smokies I had here, this is much better!
So, here we are: first part. This is a bit of steel which should probably not have that name. It cuts like butter, which is good for my confidence!
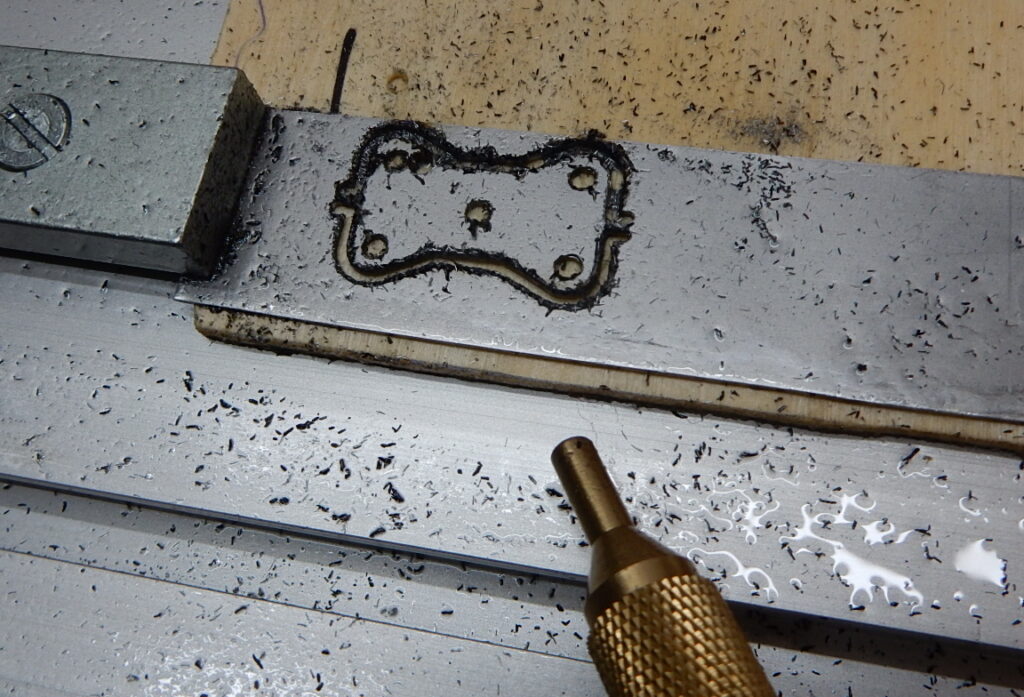
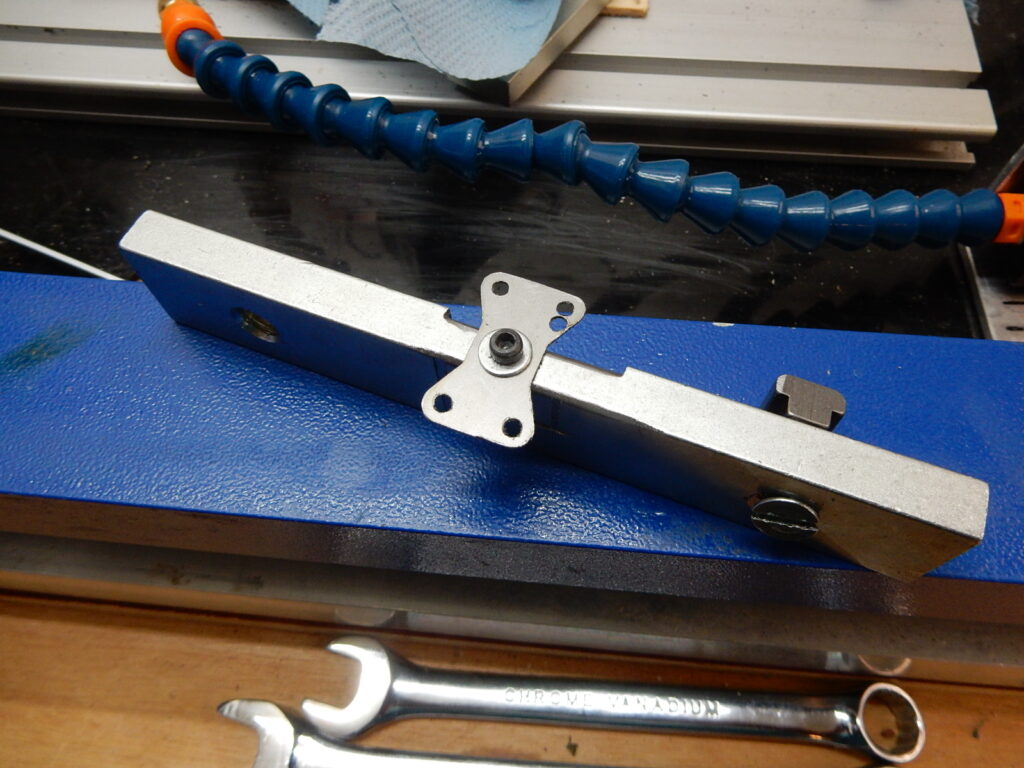
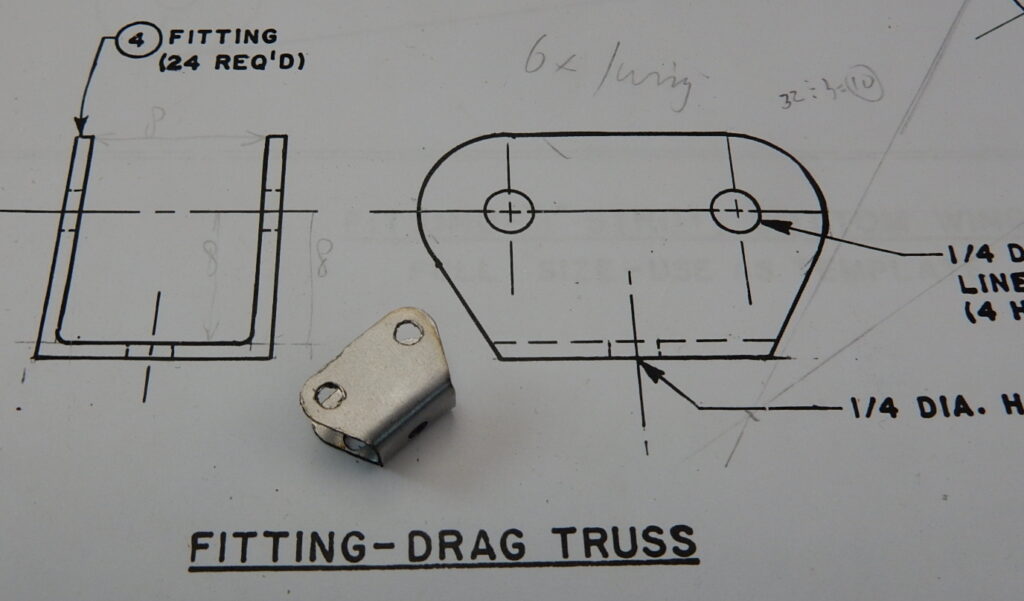
The observing reader will notice that my hole sizes are off. Original is 6 mm bolts, scaled would be 2 mm. I feel that’s a bit thin. I’ll use standard 3mm ones , marked 8.8= 800 Newton/mm2.
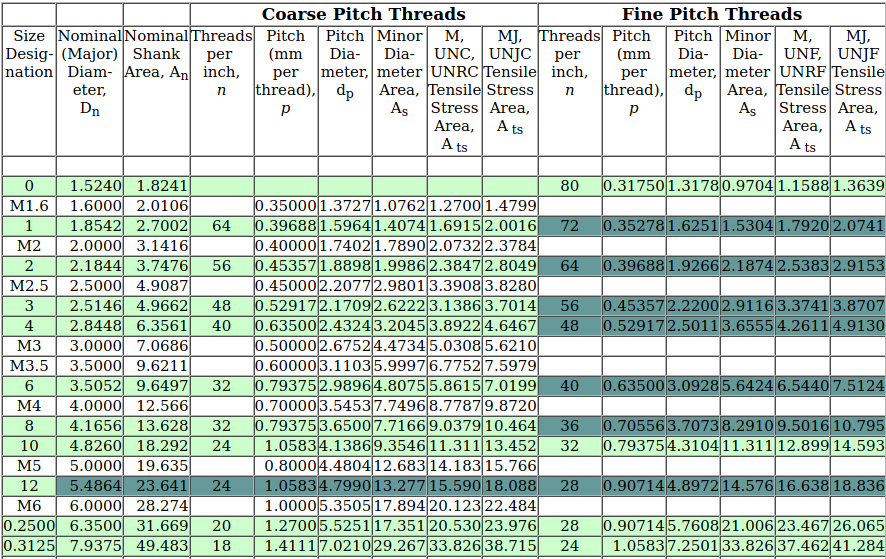
- M2, core area is 1.8 mm2. 1.8 * 80 =144 Kgf.
- M2.5, core area is 3 mm2. 3.0 * 80 = 240 Kgf
- M3, core area 4.5 mm2. 4.5 * 80 = 360 Kgf.
(not sure I have the right table here, check later! Values feel about right though) See here and this one
Ok, I’ll drill them 2.0 for now, looks like that is really enough. I’ll leave the one going through the spar at 3 mm, makes life easier. Yeah, I know, you should sort this out BEFORE cutting metal. Me thinks I’m due for a coffee break!
Trying with 0.6 mm stainless steel. It’s shiny, no other identification. Problem 1: it does not stay down on the board very well, so I really need a DOWN cut bit. (learned that in a hurry!) Not to be stopped that easy, I went slow, lots of cooling fluid, and managed these 2 parts. Progress is being made by counting the bits that did not work. Also, because the sheet is not fixed properly, I get some chatter, visible on the edges and general outline. All to be expected and just needs time to fix. I think it would also be better to have the cooling nozzle fixed to the head, moving around by hand as we go is possible, but not great.
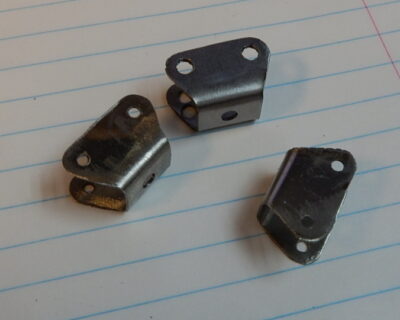
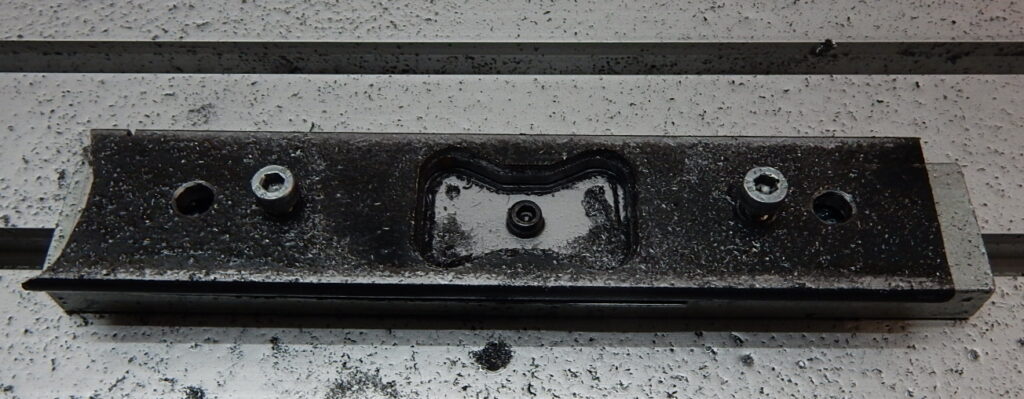
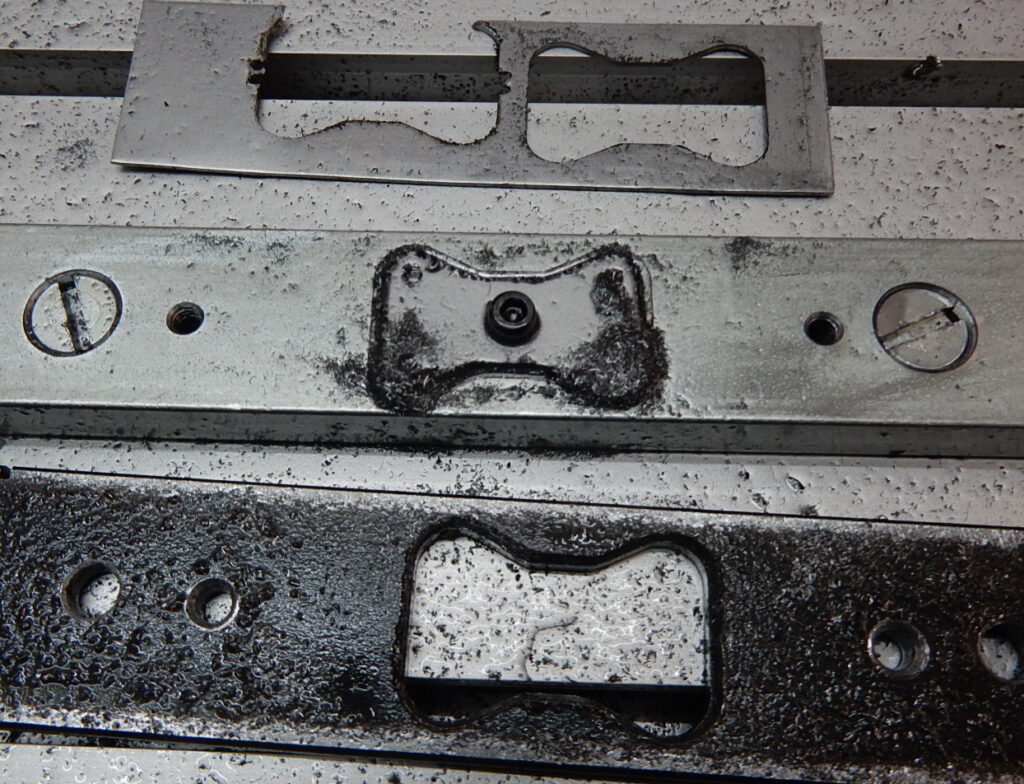
what a mess…..